Blow Moulding Applications
The costs in blow molding are lower as compared to injection molding because machinery costs are typically lower as well. In blow moulding process, one-piece construction is done so that there’s no need to connect part halves, which can achieve shapes that injection molding cannot produce
NEED FOR BLOW MOULDING
TYPES OF BLOW MOULDING
A) Extrusion blow molding(one stage)

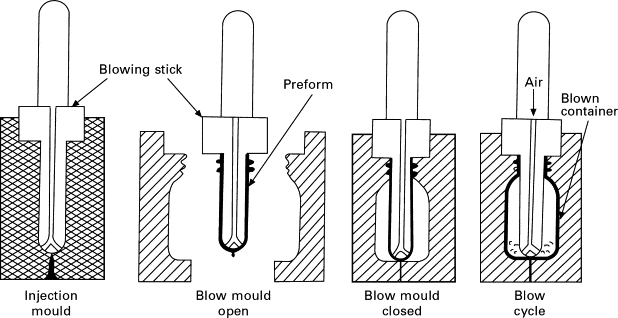
B) Injection blow molding (one stage)
C) Injection stretch blow molding (two stages)
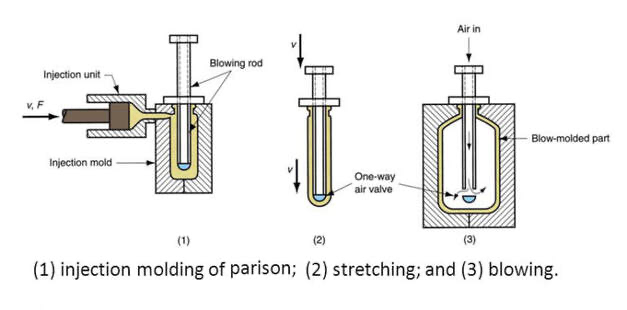
Advantages of Using Bajaj Masterbatch for Blow Moulding

Ability to handle complex part

Fast Production Rate

Enhanced Strength

Increases the tensile strength

High level of producivity

Low Costs

Instead of having pre coloured compounds, usage of our masterbatches facilitates low stock holding as and when required.
Compared to compounds, our masterbatches gives a choice of wide range of colors and other properties besides saving huge cost as the inventory level & space required is very minimal .
Provides “dust free” environment without any health or safety risks in comparision to conventional usage of pigments powders & additives individually.
Optimum dispersion of pigments and additives in our masterbatches facilitates ease of processing. Also, it reduces the cost of purging & flushing .
Elimination of ‘trial and error’ development or formulation work, as this is done already by us ensuring color strength and consistency forever.
Our masterbatches are filler free and they are fairly highly concentrated (in comparison with the target composition), with “let-down ratios” affordable and economical as per the client’s application requirements.

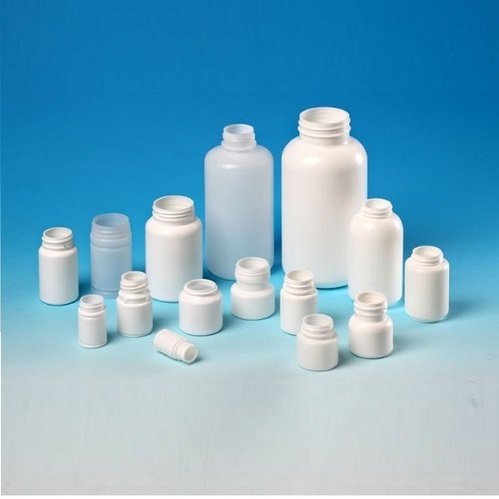
Provides aesthetic appeal with gloss and brightness on the finished product without any surface defects.
As blow moulded bottles, containers, carboys and drums are extensively used in Pharma and Chemical applications, our masterbatches has the ability to maintain the chemical stability of the pigments and other ingredients incorporated in it. This facilitates migration resistant , leaching free and non reactive & ease of using at any conditions.
We use eco friendly pigments which are not harmful to the environment, on request we can provide ROHS (Restriction of Hazardous Substance) compliance.
Ease of consolidation with polymer at any addition levels and has uniform dispersion.
They are suitable for food contact applications as the ingredients used in it are non-toxic , non hazardous and the articles incorporated with our masterbatches are safe for use.



ONE STOP SOLUTION FOR BLOW MOULDING PROBLEMS / DEFECTS
Product Solutions for Blow Moulding
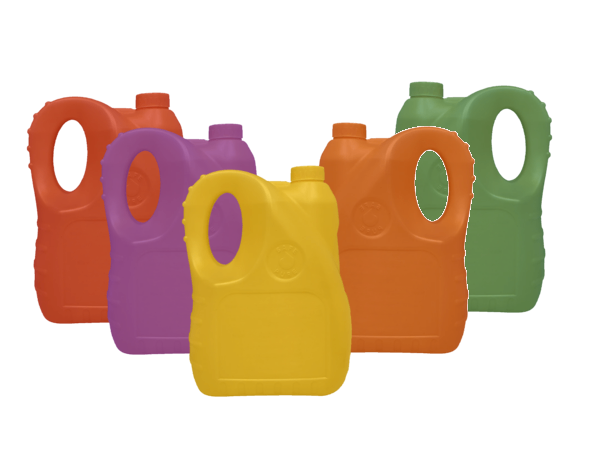
Blow Moulding Applications for
Color Masterbatch
Blow Moulding Applications for
White Masterbatches

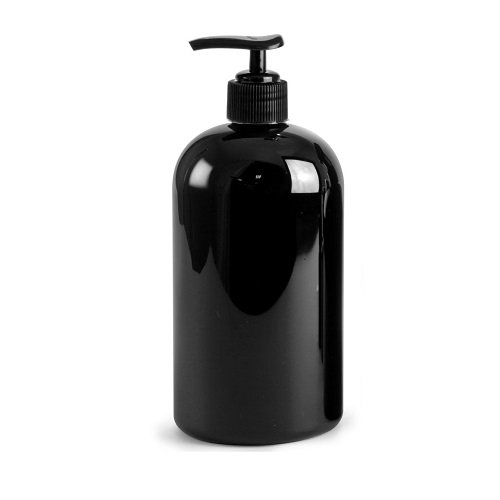
Blow Moulding Applications for
Black Masterbatch
Blow Moulding Applications for
Transparent Masterbatch

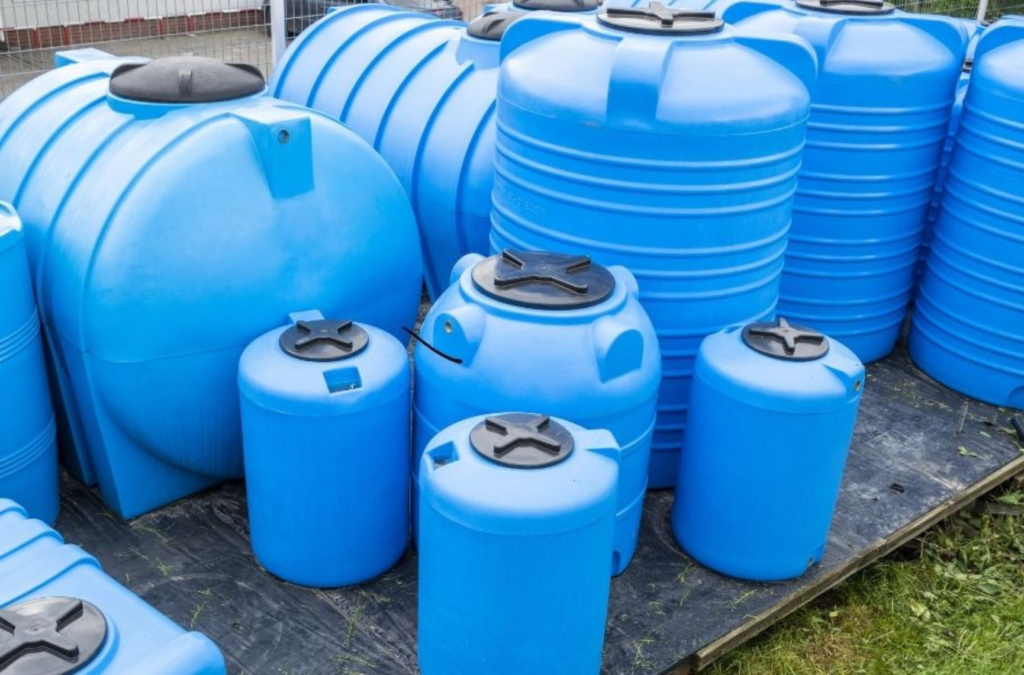
Blow Moulding Applications for
Antimicrobial Masterbatch
Blow Moulding Applications for
Polymer Processing Aid
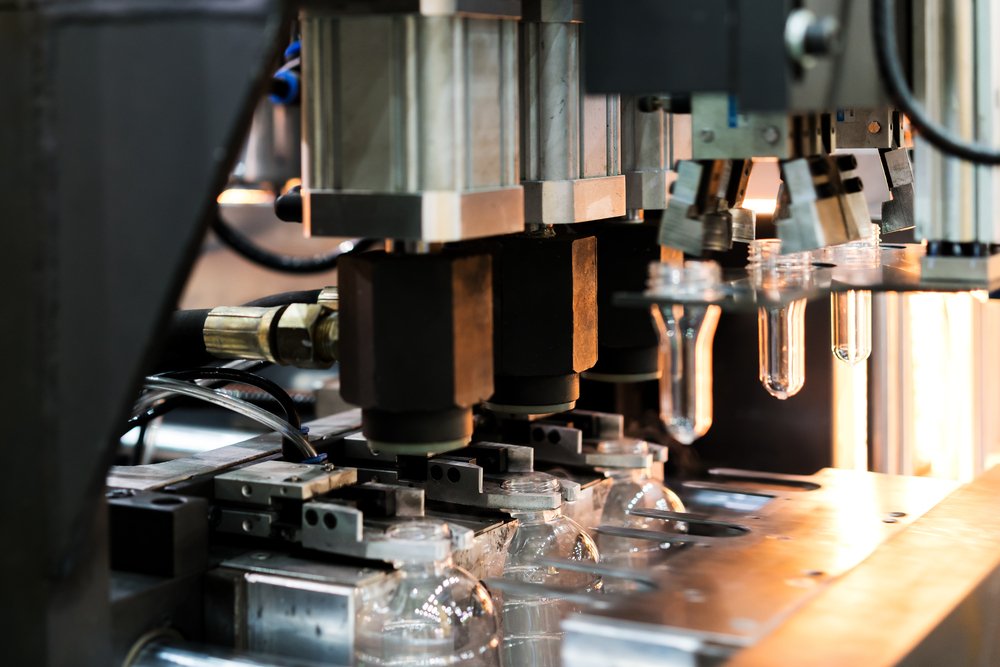

Blow Moulding Applications for
Antistatic Masterbatch
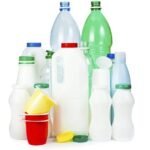


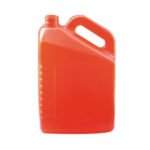

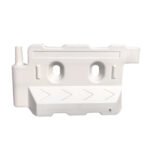

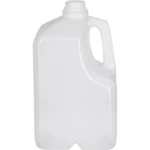

