EXTRUSION
COATING
Extrusion coating is the coating of a molten web of synthetic resin onto a substrate material. It is a versatile coating technique used for the economic application of various plastics, notably polyethylene, onto paperboard, corrugated fiberboard, paper, aluminium foils, cellulose, Non-wovens, or plastic films.

Extrusion lamination brings two films together using a layer of molten resin extruded through computer-controlled extruder dies with advanced gauge controls (nuclear gauge monitoring and automatic profile control). The two films and the molten resin form a multilayer flexible packaging lamination.
In the extrusion coating process an extruder forces melted thermoplastic resin through a horizontal slot-die onto a moving web of substrate. The resulting product is a permanently coated web structure.


Extrusion coating operations use high melt temperatures to lower the melt viscosity. This improves coating thickness uniformity and adhesion. On-line gauging is used in some operations to measure the film thickness.
Benefits of extrusion lamination

Cost-effectively adding rigidity or thickness.

Enhancing barrier properties (depending on the resin , mostly LDPE is used)

Greater puncture resistance.
Why Bajaj ?

Our mission is to ensure our customers get convinced on our batch to batch consistency as they admire us for aesthetics in the final product , high purity, temperature stability, weather fastness, Zero moisture & contamination , long term endurance and so on.
Unique features

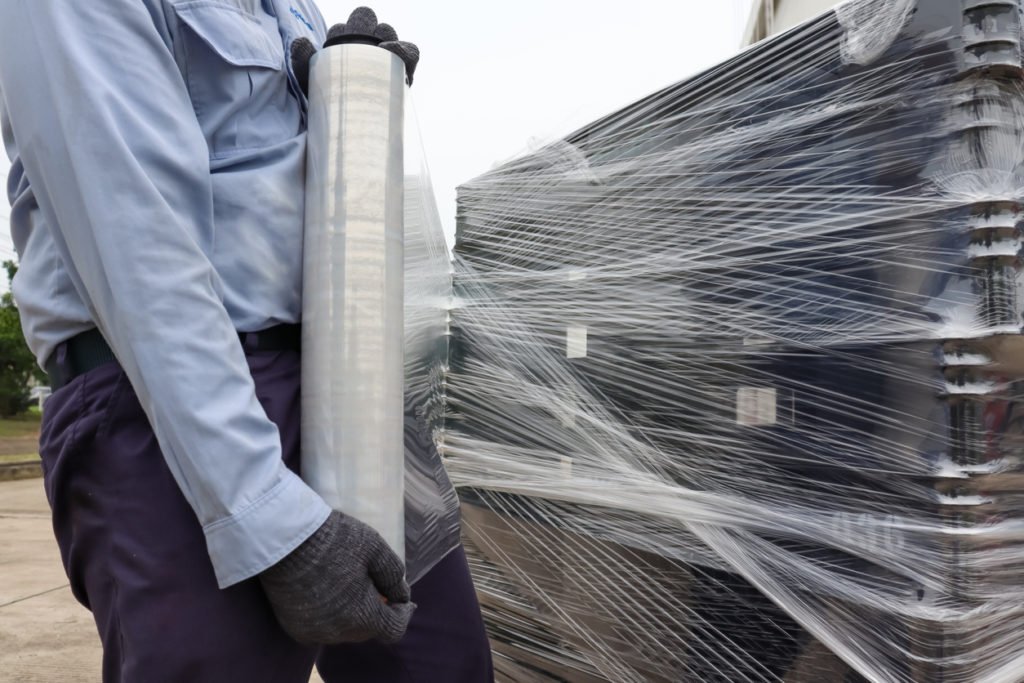



We at BAJAJ offer below products to cater this segment :
Product | Description |
---|---|
PLAST FAB | Specialized fillers made with finest particle size of CaCO3 have been designed solely for this extrusion coating / lamination application on PP fabric / HDPE raffia with LDPE coating so as to make our customers delightful & chosen us as their favorite source for many years. |
PLAST SUPER WHITE | Made with pure TiO2 , Free from filler & agglomeration gives excellent Opacity, whiteness, brightness , gloss & smooth finish on the substrate. |
PLAST ANTISTAT | To prevent dust pick up and building of static charges on the substrate. |
PLAST MODIFIER | With a combination of CaCO3 & Elastomer to give mechanical strength, smooth surface , facilitating adhesion / bonding to prevent de-lamination, improving sealing properties, barrier properties, dart impact strength , puncture resistance and so on. |
Trouble shooting guide
PROBLEM | POSSIBLE CAUSES | SOLUTIONS |
---|---|---|
Poor Adhesion | Less Polymer melt wetting on to the substrate. | Increase temperature upto 300c for LLDPE & 260c for PP. Check the heater elements. |
Less chemical bonding | Increase air gap between die and nip roll for better bonding or reduce line speed. Increase LDPE blend percentage with PP for PP fabric coating or LLDPE blend % for HDPE raffia fabric coating . |
|
Polymer melt cooled due to low chill roll temperature. | Reduce chill roll temperature. | |
Void in polymer melt. | Pre-heat to avoid volatile content in the polymer material. | |
Pin holes | Substrate roughness. | Make fabric substrate with better smoothness. |
Low coating weights. | Ensure uniform coating thickness. | |
Surging | Bridging in hopper & screw | Check on proper screw design,L/D ratio |
Edge Tear | Irregular flow of melt through die. | Set proper temperature & condition of the die ends. |
Excess draw down | Reduce line speed | |
Draw Resonance | Non-uniform thickness in machine direction | Decrease the die gap or increase the coating thickness. |
Polymer degradation | Set proper temperature profile | |
Rough wavy appearance | Improper material mixing | Select similar rheology blend |
Poor purging | Flush it thoroughly | |
Polymer degradation | Set proper temperature profile | |
Breaks Molten curtain | Draw down too low or too high | Set proper line speed |
Neck - In | Irregular flow across die | Reduce line speed |
Reduce melt temperature | ||
Select high MFI or low density material. |